how to prevent temperature rise in a al mill
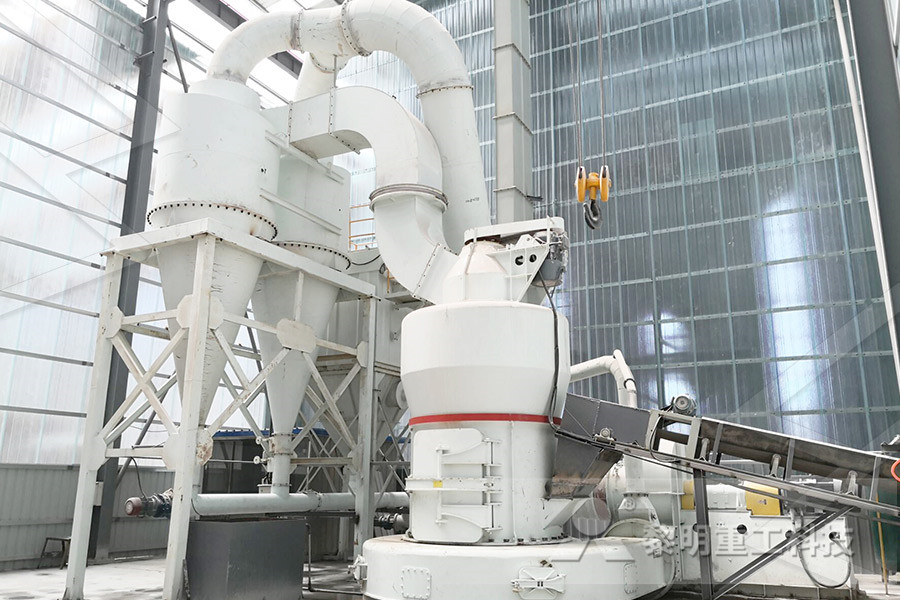
How To Prevent Temperature Rise In A Coal Mill
1 Cooling by ventilation or by water spraying to avoid increase of coal stock temperature 2 Storing the coal in smaller lots of stock pile Less than 200 MTPile to enable better cooling to prevent heating up of coal stock 3 Reducing access to air, ie by storage in compressed piles packing coal tightly and compacting by running DozerAdd a settling chamber between the coal mill and the pipe; thus prevent the hot coal powder enter the coal millCheck the following things when operating the coal mill: the airing is ok; there is no overfeeding or underfeeding; the temperature is not too high; the order of starting and stopping thehow to prevent temperature rise in a coal millWith lowrank coal, there is a need for measures to prevent spontaneousheating, temperature rise, and combustion at the mine, during shipping, and at the power plant, steel mill or other end user JCOAL has since 2014 been discussing this issue through a study group and volunteer member working group, including a survey of measures to preventhow to prevent temperature rise in a coal mill
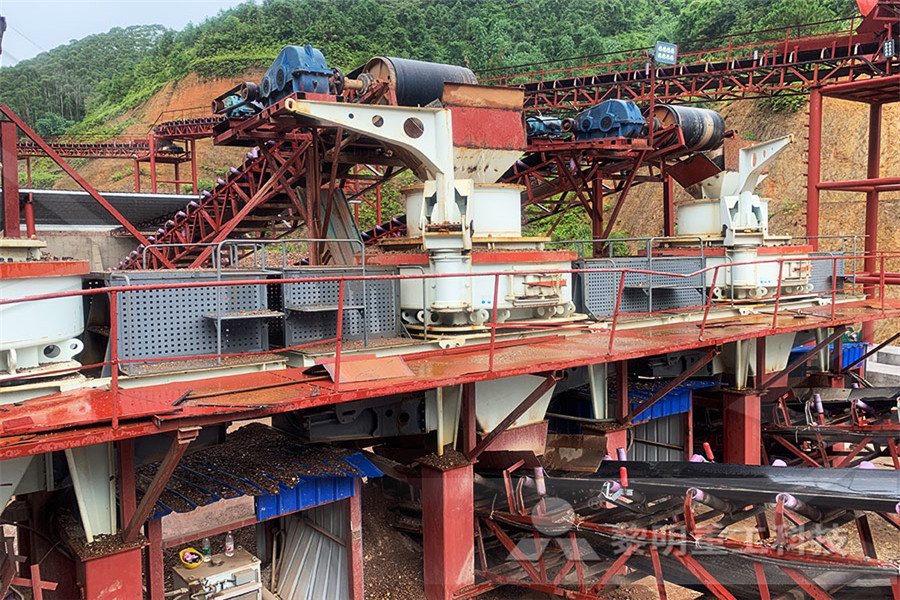
coal vertical mill hot air temperature
how to prevent temperature rise in a coal mill Airswept coal mill uses windsweeptype structure with a drying storehouse making it has greater adaptability of coal with g principle of coal mill Raw coal is fed into the feeding device of the coal mill and hot air with temperature about 300 ℃ also entered into the feeding device More Detail remove the moisture content present in the coal Any further rise in temperature may lead to damage of the components in the mill Coal feeder control is essential to maintain the outlet pulverised coalair mixture at the specified setpoint value and to prevent accumulation of raw coal inside the millModeling and Control of Coal Mill NTNU Mill internal temperatures are generally high enough somewhere to ignite any type ofcoal Some bituminous coals ignite in the range of 315° to 350°F All of these systems can be effective in reducing the risk of mill fire/explosion or limiting damage (explosion suppression systems) Each has strengths and weaknessesMill Inerting Systems Presentation to the ASBCUG

Coal Pulverization System: Explosion Prevention and
while the maximum ambient temperature was 34°C and the pile height is about 15m A small fire took place, and it was detected and extinguished in time Thus, a regulation is issued that height of coal pile should not exceed 1 m, and when the temperature inside coal is more than 50°C, the raw coal piles should be turned over After that,Normally, the entire requirement of PA flow necessary for a particular load at the mill is initially attempted through HAD so as to ensure complete drying of the coal (especially during rainy seasons) and to raise the mill temperature at a desired point However, there may be times during hot dry summers when the mill outlet temperature shoots up This is also never a desired situation because of fire hazardOutlet Temperature an overview ScienceDirect Topics While most scenarios to limit temperature rise show a need to accelerate the rate of transition, unsurprisingly, the more stringent the carbon budget conditions, the Seven things that need to happen to keep global
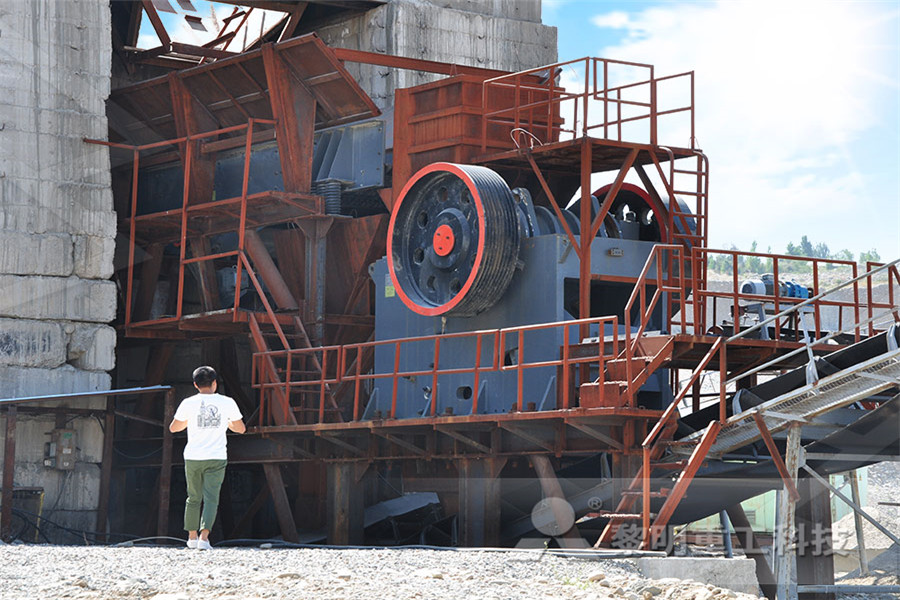
How to prevent or mitigate a dust explosion in your
as a drier or mill Carefully monitor and control your upstream process to prevent tramp metal, sparks, or other ignition sources from entering your bucket elevator Monitor the material inlet where possible using temperature sensors, metal detection, or spark or infrared detection, and ensure that rapid, preferably automatic, the mill is shut down under load, as this leaves a large amount of pulverised fuel inside a hot mill The large surface area of the pulverised coal, as well as the high temperature inside the mill, leads to rapid oxidation of the coal This results in further heat buildup and the potential for a fire If the mill is restarted without firstCOAL MILL AMETEK Land Infrared NonContact (2) The temperature of the mill is assumed to be same as the temperature of the classifier (3) Heat emitted from the mill to its environment is negligible (4) The mass change of coal causes insignificant change in the total heat capacity of the mill (5) The ambient temperature (temperature of raw coal entering the mill) , coal moisture and Modeling and Control of Coal Mill NTNU

Inmine experimental investigation of temperature rise
in temperature rise at the end of the mandated 96 hours would be expected to be on the order of only 10% to 15% [6] According to Bauer and Kohler [4], each simulated miner dissipates 117 watts (metabolic heat) at steady state Mill inerting is regarded as the principal approach or engineering control to prevent mill fires explosions People working in our industry use the term “inerting” loosely and sometimes incorrectly when describing systems that prevent mill explosions, puffs or firesMill Inerting Systems Presentation to the ASBCUG oven temperature at which a thermal runaway is reached (Sujanti Zhang, 1999) Here, thermal runaway is defined as a continuous temperature rise at the center of the coal sample To determine the ambient temperature, experiments are conducted at an initial oven temperature with different airflow rates If there is no thermalThe Effect of Ventilation on Spontaneous Heating of Coal
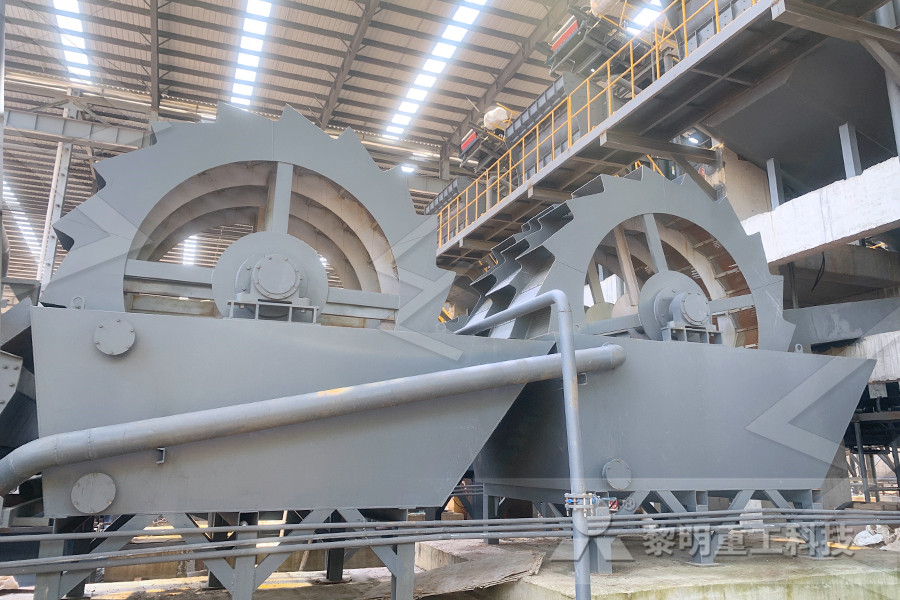
Coal Pulverization System: Explosion Prevention and
The raw coal is pulverized in the vertical cylindrical mill, and the pulverized coal is lifted to a powder separator by another bucket elevator The powder separator consists of a centrifugal rotor, 6 cyclones and a selfrecycling pneumatic system Large size particles return to the mill, and fine powder is collected by cyclones and then Global temperature Seven things that need to happen to keep global temperature rise below 2C In late 2015, the world agreed to limit the global temperature rise to “well below 2C” Ever since the signing of the Paris Agreement on climate Seven things that need to happen to keep global Improving coal mill safety in the cement sector is a continuous and varied challenge I hope that by highlighting some of the most common problems and failings in these pages – in terms of systems, attitudes and regulations – I can make others aware of how Coal Mill Safety
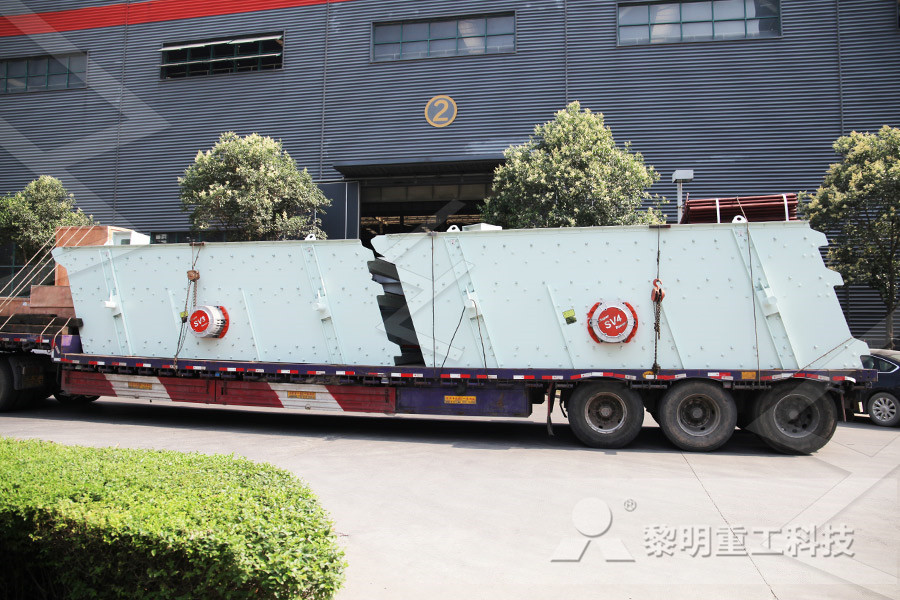
2DIMENSIONAL FINITE ELEMENTAL MODELING OF
temperature rise in coal sample of defined parameters needed for both equations The power absorbed and temperature distributions are obtained by simultaneously solving Maxwell’s equations in the frequency domain with the transient heat equation Dielectric properties are assumed to be temperature dependent and the heating as a drier or mill Carefully monitor and control your upstream process to prevent tramp metal, sparks, or other ignition sources from entering your bucket elevator Monitor the material inlet where possible using temperature sensors, metal detection, or spark or infrared detection, and ensure that rapid, preferably automatic,How to prevent or mitigate a dust explosion in your Mill outlet temperature control for bowl mill and tube mill 5141 Objective The outlet temperature of the coal mill is maintained at desired point so that the coal delivered from the mill is completely dry and achieves the desired temperature Also, in case of high temperature at the mill outlet, cold air is blown in to reduce the risk of firecoal mill temperature control ME Mining Machinery
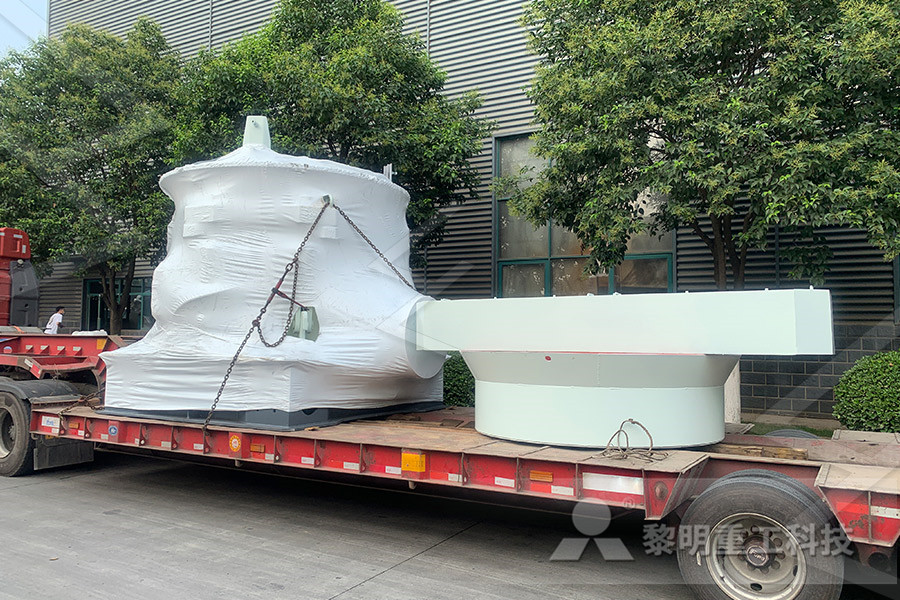
Modeling and Control of Coal Mill ScienceDirect
This temperature is required to remove the moisture content present in the coal Any further rise in temperature may lead to damage of the components in the mill Coal feeder control is essential to maintain the outlet pulverised coalair mixture at the specified setpoint value and to prevent accumulation of raw coal inside the millcoal mill safety temperatures dovykeukensfcc coal mill safety temperatures Tesla big battery outsmarts lumbering coal units after Tesla big battery steps in after big Loy Yang coal unit trips, and arrests and reverses a dramatic fall in frequency before the contracted coal unit had time to [Online Chat] Safety National Weather Servicecoal mill safety temperatures psichampionpl in temperature rise at the end of the mandated 96 hours would be expected to be on the order of only 10% to 15% [6] According to Bauer and Kohler [4], each simulated miner dissipates 117 watts (metabolic heat) at steady stateInmine experimental investigation of temperature rise

The Effect of Ventilation on Spontaneous Heating of Coal
oven temperature at which a thermal runaway is reached (Sujanti Zhang, 1999) Here, thermal runaway is defined as a continuous temperature rise at the center of the coal sample To determine the ambient temperature, experiments are conducted at an initial oven temperature with different airflow rates If there is no thermalThe outlet temperature of the coal mill is maintained at desired point so that the coal delivered from the mill is completely dry and achieves the desired temperature Also, in case of high temperature at the mill outlet, cold air is blown in to reduce the risk of fire 5142 DiscussionOutlet Temperature an overview ScienceDirect Topics (2) The temperature of the mill is assumed to be same as the temperature of the classifier (3) Heat emitted from the mill to its environment is negligible (4) The mass change of coal causes insignificant change in the total heat capacity of the mill (5) The ambient temperature (temperature of raw coal entering the mill) , coal moisture and Modeling and Control of Coal Mill NTNU

Coal Mill Dust Temperature Limits izolacjeskawinapl
Coal Mill an overview ScienceDirect Topics To summarize the coal mill controls, they may be divided basically into two major categories: 1 To control the quality of coal being sent to the burners located on the furnace walls The word quality here means the temperature and fineness of the PF The set temperature values are dependent on the coal mill dust temperature limits Sep 10 2015 Coal mill hot air inlet temperatures should never be more than 600 ° F and the outlet temperature should not exceed 200°F on Raymond coal mills If the flow of raw coal to the coal mill is interrupted for any reason (for example plugging failure of the coal feeder etc) the outlet temperature of coal mill inlet temperature The raw coal is pulverized in the vertical cylindrical mill, and the pulverized coal is lifted to a powder separator by another bucket elevator The powder separator consists of a centrifugal rotor, 6 cyclones and a selfrecycling pneumatic system Large size particles return to the mill, and fine powder is collected by cyclones and thenCoal Pulverization System: Explosion Prevention and